基于激光测距的船体分段焊缝自主寻位
作者:刘源;刘芳;马宏波;林涛;朱振友
目前,高度柔性化和自动化的船舶焊接系统在提高造船的质量、大阳城娱乐以及降低产品制造周期和成本方面具有重要的作用。在船体分段焊接过程中,大型船体内底分布着的纵桁和肋板组成了大量的格子间型结构,这些分段的格子间型结构的底板与侧板主要靠焊接的方式实现连接,单独的格子间型结构件分别包含4个平角和4个立角的焊缝。由于实际情况需要或装配差异以及不确定因素等原因,传递的格子间型虽然形状相似,尺寸大小却不尽相同。而目前市面上大多数自动化设备均是针对单一尺寸的标准产品,焊接系统柔性化较低,针对这种形状大致相同但尺寸不一的结构件,大多数自动化设备都难以实现自动焊接。
针对这种尺寸差异较大的格子间型结构的焊缝寻位,目前部分船厂采用接触式传感焊接方法。它是将带油电压的焊丝向工件移动,当焊丝和工件接触时,焊丝和工件间的电位差变为零,通过程序计算出实际位置,从而获得焊缝轨迹,。但是,这种方法的机器儿焊接系统柔顺性比较差,当焊接下一个尺寸差异较大的格子间型结构时,初始焊位获取的周期较长,导致焊接大阳城娱乐降低。同时,也提出了一种通过离线编程从格子间型结构件的数模中提取出焊缝轨迹,经软件处理生成焊缝轨迹,从而实现焊缝自主寻位的方法,但此方法获得的轨迹误差较大,有一定的局限性。
本文将柔性化焊接机器人技术集成与机器人平台载体,借助
激光测距传感器与采集卡等外部设备,对格子间型结构侧壁进行扫描,提取特征点,通过工控机的算法处理后生产工件焊缝轨迹,从而达到焊接系统的高度柔性化,实现对格子间型结构件自动化焊接的目的。
1、系统架构
机器人系统主要包括硬件系统和软件系统两部分。其中硬件系统主要包括ABB六轴机器人及其控制柜、激光测距传感器、1710采集卡以及工控机等;软件界面是利用C#语言和ABB机器人SDK工具所开发的人机交互界面,该软件界面能应用于机器人扫描过程和焊接过程的控制,机器人扫描结束后将自动生成离线的焊缝轨迹程序,并自动导入机器人控制系统。
利用固定支架将激光测距传感器和焊枪固定在机器人末端,通过采集卡将激光测距传感器采集的数据传递给工控机,机器人与工控机之间采用以太网进行通讯。系统工作时,机器人运动到初始扫描位置,激光光线设在格子间型结构的侧壁上,激光器将采集到的模拟量通过采集卡传给工控机,同时,机器人获取机器人末端实时位置的坐标值。如此,攻坚的每个侧壁均扫描两次,工控机上的软件系统将激光器测量数据与机器人采集的坐标数据进行处理,得到焊缝轨迹后自动生成离线的机器人程序。本文所用到的激光测距传感器的线性度为加金0.25%,输出电压范围为-5-5V,通过线性回归将模拟量电压值转换成距离值。
由于船体的格子间型结构件的侧板和底板大多是厚度为10-32mm的钢板,板件的接缝直线度良好。利用机器人指令Movel对焊缝轨迹进行编程,焊接速度和转角半径可根据焊接经验设定,只需获得机器人焊接时的起弧位置和收弧位置。对于4条平角焊缝,获得4个底角的坐标值和侧板的高度即可获得各焊缝的轨迹,侧板的高度需手动输入。
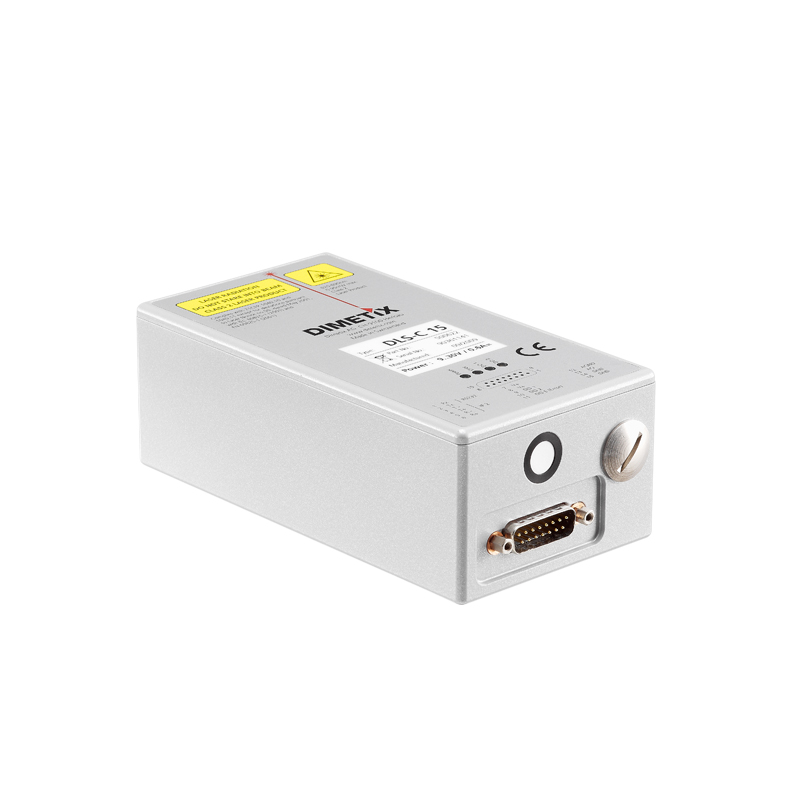
2、激光器坐标系的标定
在工控机处理数据的过程中,由于需要将激光器采集的距离值与机器人获取的坐标值进行计算,就必须要确定激光器坐标系与机器人末端坐标系的位置和旋转关系,这样才能根据机器人末端相对于机器人的基坐标系的坐标向量,得到激光器坐标系相对于焊枪坐标系的相对关系。这里将激光发射光束视为末端工具,而光束上距离激光平面为300mm的点则视为TCP,采用六点法对其进行标定。其中,采用特别设计的激光器安装支架,使激光器的发射光束与法兰盘坐标系y轴平行。
激光器位置标定过程如下:受限在桌面上固定一标准球,在球面上做一个标记点,然后示教机器人采用4种不同的姿态,尽可能使4种姿态的差异更大;同时,在调整的过程中使激光光束直射球面上的同一标记点,且各姿态下的激光测距都为300mm。
激光器的位置是激光器坐标系在空间中相对于机器人末端坐标系偏移的位置,而激光器的姿态是其相对于机器人末端的旋转关系,需要进一步确定。将激光器固定,使激光发射光束与法兰盘y轴平行,即确定了激光器坐标系的一个坐标轴的方向;而坐标系的另外2个坐标轴的方向并未确定,理论上绕激光器坐标y轴任意旋转的坐标系方向均可以称为激光器姿态标定的解;若不对姿态进行标定,泽会出现无数组解。提供了一种借助于外界辅助装置与激光器的姿态进行标定的方法,但是,辅助装置的引入会增加标定的误差,对于本文精度要求较高的系统并不适用。本文采用的方法是将激光器坐标系与机器人末端的坐标方向默认一致,在ABB机器人控制器里定义激光器坐标系的方向与法兰盘一致,可以认为激光器坐标系是机器人末端坐标系平移后的结果。按照上述过程就得到了激光器坐标系相对于法兰盘的姿态。
3、试验与分析
本文所开发的机器人系统刚才用模块化的设计思路,利用激光测距传感器进行测距,采取样点,通过编写的程序进行计算,得出焊缝轨迹,实现了整个系统按照其功能进行转换与调节。基于位移激光测距寻找焊缝轨迹的精度取决于激光器测量、系统钢结构以及标定给结果等,不可控的影响因素较多,所以,对系统扫描计算得到的轨迹的准确性需要进一步分析。
格子间型结构平角焊缝主要是由其4个底角坐标构成的直线轨迹,而立角焊缝轨迹也是在4个底角坐标基础上得到的直线轨迹。所以,通过系统扫描计算得到的4个底角坐标的精度在寒风轨迹重现的过程中至关重要,在进行系统精度分析时,重复性是系统至关重要的误差指标。
系统的重复性是指机器人系统在不改变任何条件下,按照统一方法步骤,再次达到同一轨迹位置的能力。本系统的重复性分析需要对检测出的焊缝轨迹底角坐标的一致性进行分析比较。再不改变系统部件和试验条件下,利用4个底角坐标值对轨迹进行描述。由于装配、机器人重复定位、激光测量等误差原因,造成了4个底角坐标的精度并不完全相同。通过50次重复扫描试验得到4组坐标值,一个底角对应1*50个坐标值,将各坐标值与人工测量值进行对比,得到各误差值,将各坐标的误差取均值,得到各底角的精度。精度最高的是第2个底角,为0.3358mm;精度最低的是第3个底角,为0.63978mm。船体分段焊接大多都是厚板角焊缝焊接,精度在0.5mm范围内的焊缝轨迹均可较好的满足焊接要求。
为了进一步准确的表示系统的重复性指标,针对单独一个坐标的重复性进行估算,运送标准差分析魔心归队新高精度的不确定度进行分析。采用Bessel公式来建立典型系统重复性分析的标准差模型。
再利用极差值来反映每组底角坐标之间的最大差距。从极差可以看出各组坐标值的差距较小,在0.16mm内,同时,各组底角坐标的方差较小,收敛性好,系统的重复性很好。
4、结论
a、搭建了格子间型结构工件的焊缝寻位系统,即利用激光测距传感器配合机器人、采集卡、工控软件系统获得工件特征点信息,自动生成机器人可识别捍卫轨迹。
b、采用改进的TCP标定方法对激光测距传感器进行标定,使激光传感器得到的数据与机器人坐标数据一一对应,并进行了坐标变换。
c、对焊缝轨迹精度进行分析,标明本文集成的机器人系统所得到的的焊缝轨迹精度和重复性都较好,分别为0.4mm和0.16mm集成的机器人系统柔性化程度高、精度好,较好的解决了格子间型结构由于尺寸较多、批量较少造成的柔性化焊接难题。
本文章转自爱学术(aixueshu.com),如有侵权,请联系删除
上一篇: 静力水准系统在大科学工程中的应用及发展趋势
下一篇: 静力水准在桥梁施工竖向位移监控中的应用